MES und MOM – Intelligente Fertigung auf dem Weg zur Smart Factory
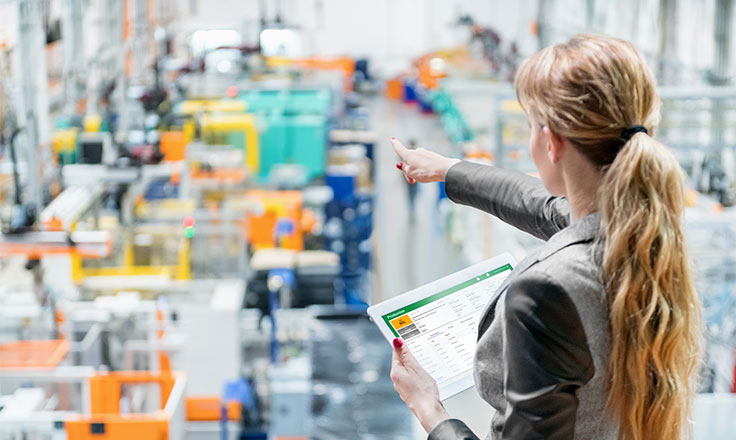
MOM ist quasi die große Mutter von MES – sie sollte auf keiner Streichliste sein, wenn geplante Investitionen auf dem Prüfstand stehen. Gerade weil hohe Strom- und Lohnkosten auf die produzierende Industrie drücken, sollte gehandelt werden. Nur wer die Datenschätze hebt, kann vom neuen Öl profitieren. Dieser Rohstoff ist zudem keinen hohen Preisen ausgesetzt: Mit Daten können alle Prozesse in der Fertigung optimiert werden. Wie datengetrieben die Zukunft der Fertigung ist, zeigt ein Beispiel aus Japan.
Innovative MES – Manufacturing Execution Systeme – entwickeln sich immer mehr zu MOM – Manufacturing Operations Management. In Zusammenspiel mit ERP, IOT, BI und KI ermöglichen MOM den Weg zur Smart Factory: Planung, Steuerung, Ausführung, Auswertung, Prognose und Optimierung der gesamten Produktion und Logistik aus einer Hand. Echtzeit-Daten werden mittels Business Intelligence oder Künstlicher Intelligenz analysiert, um daraus Handlungsempfehlungen abzuleiten. Daten und Dashboards können so die Produktion stetig optimieren. Dazu sollte MOM mit ERP-System und Maschinendaten in Form von Hubs integriert sein. Mit MOM steht ein wichtiger Schritt in Richtung Smart Factory an, jenes Idealmodell einer vollständig vernetzten Fabrik. Produktionsanlagen und Logistiklösungen lassen sich durch Einsatz von IoT MES und KI weitgehend selbst organisieren. In einer Smart Factory sind die Arbeiten der Mitarbeiter, Software, Maschinen und Roboter jederzeit transparent und in entsprechenden Datenketten dokumentiert. Diese Daten sind der Schlüssel, den es umzudrehen gilt, um sich schnellere Wege in der Fertigung zu erschließen.
(Künstliche) Intelligenz als Gehirn der Smart Factory MES: Wie können Daten und ihre Analyse die Fertigung optimieren?
Alle produktionsrelevanten Daten sollten aus den verschiedenen Quellen in einen Daten-Pool zusammenfließen. Dabei ist zu berücksichtigen, dass sowohl Software, als auch Maschinen und Komponenten berücksichtigt sind. In MOM werden ERP-Daten, IoT-Daten und MES-Daten zusammen erfasst, ausgewertet und weiterverarbeitet. Dies beschränkt sich nicht nur auf jene Software-Daten, sondern umfasst auch alle anderen integrierten Systeme wie Sensoren- und Maschinendaten. Dabei wird auf Logfiles von Maschinen zurückgegriffen, was gerade bei modernen, digitalisierten Anlagen in vielen Fällen standardmäßig möglich ist. Ältere Maschinen und Anlagen (Brownfield) können mit Sensorik nachgerüstet werden. Durch Retrofit wird der in die Jahre gekommene Teil des Maschinenparks mit dem IoT verbunden. Sensoren garantieren die IoT-Anbindung, welche wiederum auch hier die Verfügbarkeit von Daten in Echtzeit im MOM ermöglicht. Prozessdaten, Servicedaten und Ereignisdaten werden dabei durch die Sensoren übermittelt. In diesem Bereich gilt das IO-Link-System als standardisiertes Anbindungssystem für Datentransfer. IO-Link-Sensoren transportieren im Kommunikationsprotokoll zusätzliche Informationen und speichern Einstellungen zu Parametern. Dies ermöglicht den schnellen Austausch im Falle von beschädigten Sensoren. Ihre Nachfolger können während des laufenden Betriebs alle gespeicherten Informationen übernehmen. In den Dashboards werden diese Daten ausgewertet. So gibt es genaue Instruktionen, an welcher Schraube gedreht werden muss, um die Produktion und generell die OEE (Overall Equipment Effectiveness) zu verbessern. Schließlich können so die Gesamtanlageneffektivität genau ermittelt und die richtigen Entscheidungen getroffen werden, egal ob es sich um Prognosen zur mean time to repair bei Maschine A oder mean time to failure bei Maschine B handelt. Mit wenigen Klicks und Blicken ergibt sich eine Übersicht über Maschinenverfügbarkeit und darauf basierend eine effektive Steuerung der einzelnen Produktionsschritte.
Asset Tracking: Noch mehr (Bewegungs-)daten
Durch eine zusätzliche Integration von Asset Tracking lässt sich diese Analyse noch ausweiten. Mit Bewegungsprofilen von Assets kann genau ausgewertet werden, ob die Metriken der Produktion erfüllt werden und mit welchen Stellschrauben sich Prozesse verbessern lassen. So stehen für die Analyse der OEE noch viel weitreichendere Datenbestände bereit.
Mit diesen Daten lassen sich zahlreiche Vorteile erzielen. Ein MOM der Zukunft sollte es ermöglichen, die folgenden Ziele umzusetzen, die zu einer Optimierung in Produktion und Logistik führen. Bottlenecks in der Produktion können frühzeitig erkannt und mit Gegenmaßnahmen verhindert oder vermindert werden. Die Auslastung und die generellen Kapazitäten der Produktion lassen sich steigern. Eine Verbesserung des Produktionszyklus kann so erzielt werden. Mit Reduktion des Ausschusses, Verbesserung der OK/NOK- Rate können auch Materialverbrauch und Kosten reduziert werden sowie die Nachhaltigkeit in Form der Öko-Bilanz gesteigert werden. In der Summe lässt sich dadurch die Marge auf ein Produkt steigern.
Data Mining in der japanischen Praxis
Produktivitätssteigerung war eines der Ziele eines führenden internationalen Fertigungsunternehmens aus Japan, das weltweit 26 Fabriken, fünf Verarbeitungsanlagen sowie neun Forschungs- und Entwicklungszentren betreibt. Dies erforderte wirksame und effiziente Instrumente zur Analyse historischer Daten sowie zur Vorhersage sich abzeichnender Entwicklungen und Schwächen. Dazu wurden die riesigen Datenmengen aus den Produktionslinien strukturiert erfasst. Die Maschinen, die im Produktionsprozess eingesetzt werden, erzeugen sehr spezifische Daten, die mit einfachen Analysetools nicht analysiert und geschäftlich genutzt werden können. Die Nutzung dieser unstrukturierten und bisher nicht analysierten Daten ist jedoch aus Sicht der Produktivitätssteigerung und -optimierung von entscheidender Bedeutung. Zu diesem Zweck wurden Data-Mining-Lösungen in folgenden Bereichen eingesetzt: Qualitätsanalyse der hergestellten Produkte in Abhängigkeit von den Maschinenparametern, Fehleranalyse und Ursachen, die zu Ausfällen und Fehlern führen, Fehlervorhersagen, Planung und Terminierung optimaler Produktionsprozesse.
Diese Analysen von Big Data ermöglichen es, Entscheidungen zu treffen, die sich erheblich auf die Kostenreduzierung, die Verringerung von Ausfallzeiten und die allgemeine Steigerung der Produktivität auswirken.
Umgesetzt wurde zum Beispiel eine genaue Ausschuss-Kalkulation auf der Grundlage verschiedener Maschinenmodelle. Auch die Dauer der Stillstandzeiten konnte für jeden Monat und jede Maschine in Abhängigkeit von verschiedenen Typen vorhergesagt werden. Die Prognosen wurden durch Validierung der Modelle auf der Grundlage historischer Daten spezifiziert. Dabei wurden auch Parametern wie Maschinengeschwindigkeit, Schichtsysteme, Teams und Material einbezogen.
Für jede Maschine wurden unterschiedliche Methoden angewandt – für Produktionsmaschinen wurden die Daten pro Schicht aggregiert, für Verpackungsmaschinen pro Minute. Die gesamte Lösung wurde mit der Sprache R und der R Studio Plattform entwickelt. Die beschriebene Lösung ermöglichte es dem Unternehmen, Verluste zu minimieren und Produktionsprozesse so zu planen, dass die Stillstandzeiten möglichst verkürzt werden, was letztendlich zur Steigerung der Produktivität geführt hat.
MOM – Mit Daten in die Zukunft
Ein modernes MOM ermöglicht umfassende Optimierung auf Basis von Echtzeitdaten aus den Produktionsmaschinen. Berechnet werden u.a. die Gesamteffektivität, die Einsatzfähigkeit der Maschinen, aber auch Ursachen von Maschinenstillständen und die Fehlerquellen bei Produktionsausschuss. So können einzelne Produktionsschritte überwacht werden. Dazu lassen sich Regeln definieren und entsprechende Alerts einstellen.
MOM wird es erlauben, die Produktion in allen Lebenszyklen und in Echtzeit zu optimieren. Ziel ist es hierbei, die Produktqualität durch Digitalisierung innerhalb der Fertigung zu erhöhen und durch optimale Anbindung der Lösungen zur Digitalisierung den Ressourceneinsatz zu reduzieren. Insofern optimiert ein zukunftsfähiges MES die eigene Geschäftsbilanz nachhaltig. Als Investition in die Zukunft sollten MOM-Projekte daher nicht auf der Streichliste in Krisenzeiten stehen, sondern weit oben auf der Prio-Liste.
Weitere Informationen zu Industrie 4.0, MES und IoT finden Sie im folgenden Whitepaper:
Effiziente Datengestützte Digitalisierung der Fertigung